Truckin
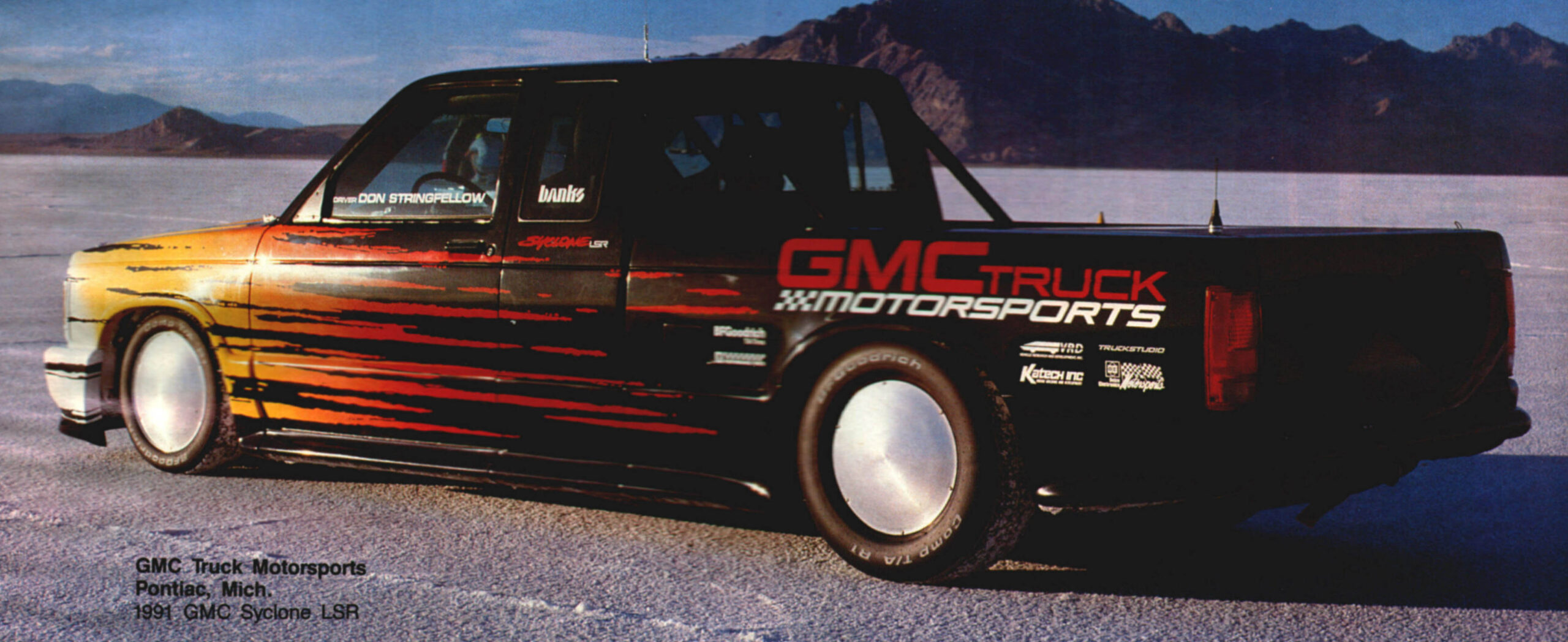
GMC sets a 204 mph record at Bonneville!
BY FRANK HAMILTON
GMC returned to Bonneville Salt Flats one year after setting a speed record in a GMC S-15 Club Coupe of 194.770 mph the flying mile for FIA category A, group II, class 9. Last year’s GMC record broke a previous mark set by the late Al Holbert in a Porsche 928. Veteran driver Don Stringfellow drove a GMC Syclone LSR this year in GM’s quest for 200 mph.
Why Bonneville?
GMC Truck Motorsports is an offshoot of GM Truck & Bus Group Advanced Vehicle Engineering and was started after GM noted a growing interest in the sport truck market. The Bonneville program developed early last year when GMC decided to make a speed record attempt with a sport truck.
The recent development of the Syclone revived the program again this year. M. S. (Mike) Kramer, Manager Compact Pickup and Variants Product Line stated, “The reason we are going back to Bonneville is simple. We want to validate work on the 4.3L V.6 as well as perform aerodynamic studies as we look toward the January 1991 introduction of the high performance GMC Syclone street machine.”
Bonneville is perhaps the best place for land speed record attempts because of its length and flatness. It is said of the Bonneville Salt Flats area that it is so flat and so large that the curve of the earth can be seen on the horizon. Matter of fact, the surface of the salt varies by no more than three inches on the Bonneville Salt Flats. A nine mile salt track allows a gradual build-up in speed needed for record attempts.
Syclone LSR
GMC Truck consulted with Gale Banks Engineering because of his well-rounded experience on Bonneville. GM also combined efforts with Katech Engineering to produce a strong race ready engine. They then commissioned Almont, Michigan based Vehicle Research and Development to prepare the Syclone LSR.
The engine is based on a production 4.3L engine which was bored and stroked to 5.0L. Many changes were performed on the powerplant to make it perform better on the salt. Perhaps the most critical engine change on this year’s truck was swapping heads which allowed increased air/fuel flow into the block. This when combined with a twin ram induction modification, made engine speeds of up to 8000 rpm possible! Compression was increased from a stock 9.3:1 to a stout 14.0:1 ratio. A dry sump oil system was also used to improve horsepower and all engine components were balanced to tight tolerances.
Since FIA sanctions restrict the use of forced induction for this class, measures were taken to increase intake charge density. Banks incorporated “cool charging” into the induction system to lower intake charge temperature thus increasing its density. Experiments were conducted prior to the record attempt using different inert gases (such as nitrous oxide) in the cool charging system. Cool charging alternatives might be used in the future but a traditional “cool can” was used on this run.
Engine management was upgraded from last year’s attempt as a more reliable Delco Electronics GEN III digital control module (ECM) was used in place of the GEN II used last year. This is the same unit used for Chevrolet Indy motors and has the distinct capability of quickly calculating air/fuel ratios for temperatures down to zero degrees Fahrenheit. Vehicle telemetry was used to monitor various running data (engine speed, intake air tempera. ture, ride height, etc.) from a remote location while the truck was at speed. (Since most inert gases produce temperatures far below zero degrees, the Delco GEN III was not able to calculate air/fuel ratios for the drastic intake charge cooling temperatures that are produced by gas cool charging procedures. This is why a traditional cool can was employed on this attempt.)
Gearing proved to be critical on the salt. A Weisman 5-speed manual transmission replaced the standard 4-speed automatic trans because more selective gearing could be achieved with the manual trans. There is a fine balance between engine speed and traction requirements and ambient temperatures will determine gearing combinations. Although the six cylinder engine used in the Syclone produced an impressive 549 horsepower at 7200 rpm, torque figures were limited to 412 lbs/ft at 6000 rpm. These peak figures mean that the truck is capable of high speeds, but acceleration in high gear is limited. Low gearing might have caused the vehicle to lose traction on the slippery salt track under heavy acceleration while high gear combinations might cause the engine to be bogged down for lack of torque. Traction was improved by adding weight to the vehicle directly above the rear wheels, but horsepower could be robbed with the addition of too much extra weight, so you can see how gearing plays a major role in speed record attempts.
Body modifications made the truck more aerodynamic Alterations include a 12.2 inch length increase and a 0.8 inch width increase. An air dam and ground effects were installed onto the body, a hard half-tonneau was mounted over the rear of the bed and Moon disks were mounted onto the wheels. When combined, these body modifications accounted for a significant decrease in the vehicle’s drag coefficient. The streamlined Syclone cut the wind with a clean .315 cd (coefficient of drag). Not only was the truck built for speed but a unique paint scheme was applied onto the body which could be best described as the look of something that had just collided with a comet.
Suspension modifications were necessary to make the truck perform well on the salt. The lowered stance was achieved with Bell Tech dropped spindles which improved handing at high speed. More weight was added to the truck to provide better traction and better handling on the salt. The final curb weight was 3585 lbs., 875 lbs more than the stock weight of 2710 lbs. BFGoodrich Comp T/A R1 radials were used for traction and measured 205/50ZR15 in front and 255/60ZR15 in the rear. The “Z” speed rating indicator found in the tire size numbers, means that these tires were designed to hold under high speed stress. The salt surface of the Bonneville is notorious for shredding tires, so it is very important to use reliable rubber on the track. Treads were shaved to 2/32 of an inch at the center of the tread area tapering to no tread at the shoulder. Since tire shredding often occurs in the deceleration stages of a run, a parachute was used to slow the Syclone down. Use of a parachute also prevents boiling the brake fluid and scorching brake pads.
The truck’s dashboard was equipped with numerous gauges so the driver can monitor pertinent engine functions. Safety items include a full rolicage, window netting, harness belt, fire extinguisher and Recaro seats.
History In The Making
For the reader who is not familiar with FIA rules, a brief description is in order. The rules state that two runs must be made in opposite directions within an hour time frame. These rules account for changes in track or weather conditions as well as any discrepancies in land inclination. This particular class record prohibits the use of forced induction, so turbos, blowers and nitrous oxide injection are not allowed. On the Bonneville track, a trip sensor is set on the fourth mile and kilometer and mile sensors are put in place to calculate kilometer and mile velocities.
Upon the arrival of the press, the Syclone had set a two way average record of 203 mph. Gale Banks was optimistic that the truck could perform even better. In fact he stated that the truck was capable of bettering 210 mph. The first two runs of the day were completed within an hour of each other as prescribed in the FIA rules. The truck traveled over the 200 mph mark, but it had not yet come close to Banks’ expectations Driver Don Stringfellow experienced some tire slippage on the East to West pass, so he was forced to shift into overdrive early. The motor was not able to pull high gear well as a result of the premature shift, so the run was not as strong as it could have been.
The truck came into base camp where the crew waited to fine tune the truck. The engine and all running gear was looked over. Data banks tucked under the rear half tonneau were checked. Banks recommended a three percent gear change which brought the final drive ratio to 3.09:1. Gale and his crew also decided to take a risk and turn the rev limiter up to an 8000 rpm ceiling. This could mean throwing the crank through the side of the engine block. The engine was ran while the ECM was monitored from the remote station housed in one of the base camp’s motorhomes. Everything checked out properly. The entire process took almost three hours. The final step was to ice down the cool can.
The third run was done West to East against a 12 mph head wind. Top speed was clocked at 198.222 mph for the flying mile. It was hoped that the wind would continue for the fourth run which happened 51 minutes later.
Unfortunately, the wind had subsided, so the run would have to be done without a favorable tail wind. Witnesses stood perched and ready for the return pass. The truck could be seen on the horizon as a rooster tail was kicked up on the salt track. The tension mounted, then the truck tripped the traps clocking an incredible 210.069 mph East to West run! The crew yelled with joy and congratulations were verbalized over the two way radios. A record two way average was established at 204.145 mph for the flying mile and 204.016 for the flying kilometer in FIA Category A, Group II, Class 9 and Class E for pickups.
One final footnote. In a post run interview with Don Stringfellow, he stated that the engine was revved out to 7920 rpm! Banks’ primitive cool can worked well too, as an intake charge temperature of 58 degrees Fahrenheit was attained at 100 degrees ambient temperature. Hats off to all contributors who helped break the 200mph barrier! In the event that GMC will return to the salt next year, you can bet that Truckin’ will be the first sport truck publication to report it to you, our readers!